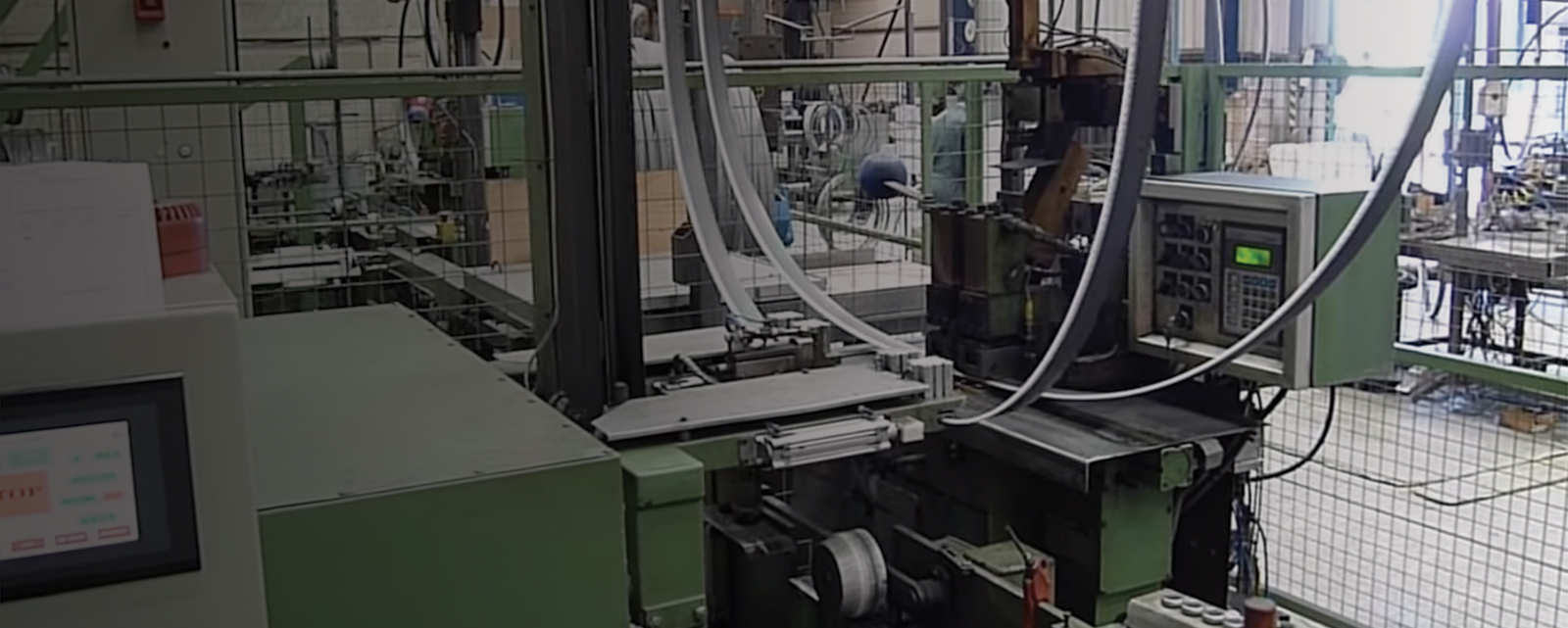
One Stop Sawing Shop | Next Day Blade Delivery
Enquiries and Support: 01706 225 221
Harrison take innovation very seriously. We have designed and developed the Automatic Weld Cell in house. The fully patented production machine gives us a large capacity meaning at peak times we never struggle to send orders out on time.
The Weld Cell is an automated blade production system that can take a range of bandsaw coils, cut and weld with the addition of edge protection all with minimal human interaction to set up. It uses soft control computer screens, and can handle blade lengths of 2.4 meters – 12 meters and widths 27mm – 67mm.
The main benefits to Harrison Saw & Tool and our customers:
No other competitor has access to this technology in the UK.
The Automatic Weld Cell was designed and developed in-house over a 4 year period and is the ultimate machine and by far the most accurate and efficient way of turning coil into a welded band. The Weld Cell is a world first and to our knowledge there is no other automated way to produce welded bands anywhere in the world.
We carry out batch sampling on the accuracy of the welds whether produced automatically or manually.
The tolerance we work with is straightness 1/2000th" or step .05mm
We have an exciting array of new products currently being introduced and in the pipeline.
Please fill out the form below and someone will contact you soon.